Powder coating is a coating with pure solid content. It can be sprayed automatically. Large or super sprayed powder can be easily collected by the recycling system to achieve the purpose of recycling. Therefore, the utilization rate of powder coatings can reach almost 100%, which enables the coating industry to reduce the cost of waste disposal and minimize the degree of environmental pollution. For decoration and protection of all coatings, coatings of different formulations can provide additional protection against UV rays, corrosion, abrasion and chemicals. Thermosetting powder coatings have become the coatings of choice for consumer products such as bicycles, lawn and office furniture, kitchen appliances and automobiles.
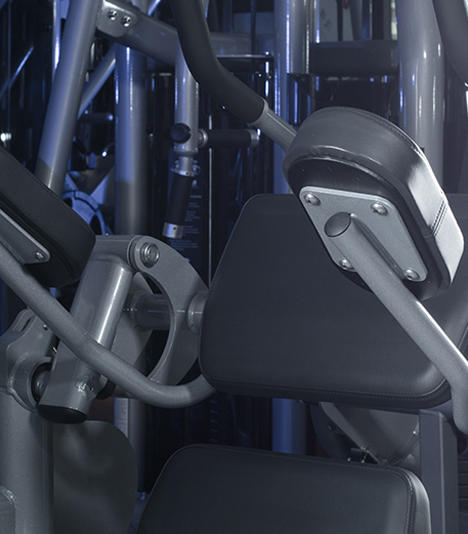
The main component of electrostatic powder is powder. The quality of the function directly affects the quality of the spraying effect, and the tool for spraying also needs to be a special spraying tool to display its real meaning. The use of electrostatic powder spray guns is related to Knowledge: It is mainly composed of several elements such as high-voltage generator, gun nozzle, gun body, controller fluidized powder barrel and air auxiliary device. To ensure that the powder particles are effectively negatively charged and have a reliable adsorption function for the workpiece, this is the tool used for electrostatic powder - the spray gun.
The spraying method can be manual, automatic or manual+automatic. 100% of the spray material is solid powder, the free powder can be recycled, and the paint recycling rate can reach 98%. Suspension transport system with high degree of automation. The coating has few micropores, good anti-corrosion performance, and can be sprayed with thick film at one time. Environmentally friendly powder coatings have no organic volatiles and avoid waste due to volatilization into the atmosphere, so compared with liquid coatings, energy costs are greatly reduced. The electrostatic spraying equipment can get a thick film in one spray, without repeated spraying or primer. It is faster and more efficient than the same film thickness. No standstill time is required in the coating equipment, which saves equipment space. In addition, the baking time of powder coating is also shorter than that of liquid coating, so it can greatly reduce the consumption of fuel and energy, shorten the coating operation line, and improve the output and production efficiency.