In the production process of powder coating manufacturers, in order to seek better powder coating quality, the powder coating storage, construction environment, and loss of light cannot be ignored.
1. Storage of powder
The storage of powder has a great influence on its quality. The powder is generally stored in a ventilated and dry place, and the temperature of the storage space should not exceed 30 degrees.
Powders of different varieties cannot be placed together to avoid mutual contamination. The powders from different manufacturers must be recycled during construction, that is to say, the next batch is used after one batch is used up, and the unused powder must be sealed in the box to avoid contamination.
2. Construction environment
Powder construction units have different environmental requirements, some are open-air, some are closed, and some are integrated with the production workshop.
The correct powder construction environment for powder coating manufacturers should be independent and equipped with powder recovery equipment. Do not put unused powder in the spray booth. Before going to get off work and after work every day, the spray room must be cleaned thoroughly with a mop or a vacuum cleaner. The dust concentration in the spray room should not be too large. First of all, it is not good for human health, and more importantly, if the powder reaches a certain concentration in a certain space, it will explode, which is very dangerous. Because the main component of the powder is chemical raw materials, which are flammable, fireworks must be prohibited in the spray booth.
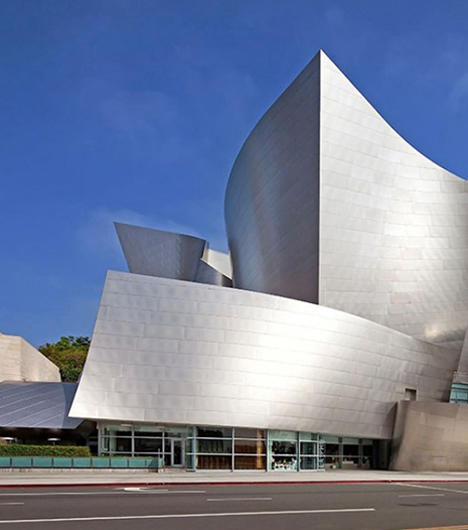
3. The phenomenon of powder loss and its treatment
(1) The surface of the powder may lose its luster if it exceeds the specified time and temperature in the oven. Epoxy polyester (indoor) powder generally has a constant temperature of no more than 190 degrees. The constant temperature of pure polyester powder generally does not exceed 220 degrees.
Because different materials require different heat energy, the time placed in the furnace is different. For example, the aluminum type, thin iron plate, etc. are generally placed in the furnace for no more than 15-20 minutes. Large metal parts, etc. are generally placed in the furnace for 30-60 minutes.
(2) In order to reduce waste during construction, the recycled powder is mixed with new powder, which often causes the surface of the workpiece to lose its luster. The correct method is to add about 3 kg to one piece of powder (normally), generally it should not exceed 5 kg, otherwise the light will be lost.
(3) The powder is agglomerated due to high temperature or excessive extrusion. This condition tends to dull the powder. In this case, the agglomerated powder is generally treated with a sieve, and then combined with the non-agglomerated powder, this problem is solved.
(4) Powders from different manufacturers are mixed with each other, and the powders will lose their luster due to mutual interference. If you need powder from different manufacturers, you must clean up the powder supply barrel, spray gun, powder pipe and surrounding environment of the electrostatic generator, and then use another powder.
(5) Generally, the powder should not be stored for too long. If the time is too long, the gloss will change. Generally, if the powder with high gloss is stored for too long, some powders will often lose gloss after construction. Powders with low luster, such as black matt, gray matt, etc., may have ripples and sand patterns after being stored for a long time.
(6) Transparent powder interferes with other powders. As long as you have used transparent powder during construction, if you want to change to other powders, you must clean the gun, powder supply bucket, and spray room thoroughly.