Pipeline powder coating is a process in which a layer of dry, powdered paint is applied to the surface of a pipeline. The powder is electrostatically charged, which allows it to stick to the surface of the pipe. Once the powder is applied, it is then cured using heat, resulting in a smooth, durable finish.
One of the main benefits of pipeline powder coating is its durability. The cured powder coating forms a strong, protective layer on the surface of the pipe, which helps to prevent damage from abrasion and impact. This makes it an ideal solution for pipelines that are exposed to harsh environments, such as those buried underground or installed offshore.
Pipeline powder coating is also highly resistant to corrosion. The coating forms a barrier between the pipe and the environment, which helps to prevent the formation of rust and other forms of corrosion. This is especially important for pipelines that carry corrosive materials, as the coating helps to prevent leaks and spills.
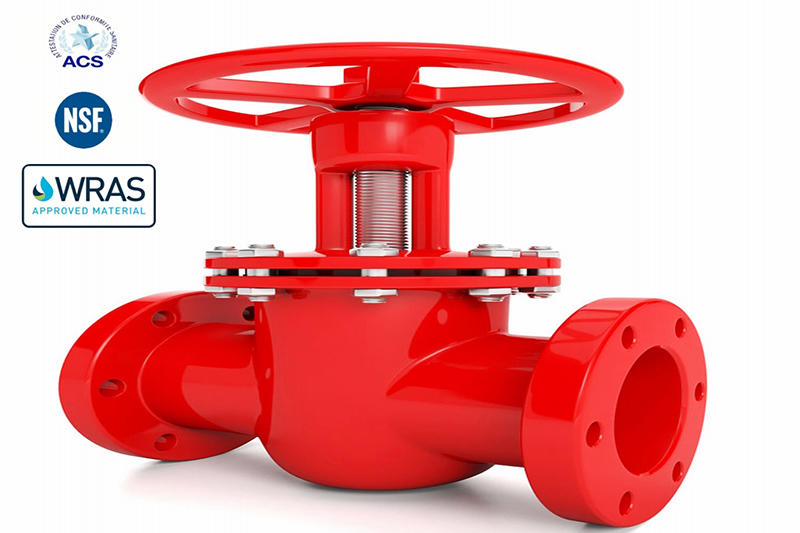
In addition to its durability and corrosion resistance, pipeline powder coating is also highly customizable. The powder can be mixed with a variety of pigments and additives to create a wide range of colors and finishes. This allows businesses to choose a coating that meets their specific needs and preferences.
Pipeline powder coating is a cost-effective solution for protecting pipelines. It is a more affordable option compared to other corrosion-resistant coatings, such as galvanization or ceramic coatings. It is also faster to apply than these alternatives, which can help to reduce downtime and increase efficiency.
Overall, pipeline powder coating is a durable and corrosion-resistant solution for protecting pipelines. Its customizable nature and cost-effectiveness make it an attractive option for businesses looking to protect their pipelines from the effects of corrosion and other forms of damage.