Thermoplastic powder coatings, which have been around since 1950, melt at the spraying temperature and solidify into a film when cooled. Due to the simple processing and spraying methods, powder coatings only need to be heated, melted, leveled, cooled or extracted and solidified to form a film, and no complicated curing device is required. Most of the raw materials used are common polymers on the market, which can meet the performance requirements under most conditions. However, there are some deficiencies, such as high melting temperature, low coloring level, and poor adhesion to metal surfaces. Nevertheless, commonly used thermoplastic powder coatings still exhibit some unique properties, among which polyolefin powder coatings have excellent solvent resistance; polyvinylidene fluoride coatings have outstanding weather resistance; polyamides have excellent abrasion resistance; Vinyl chloride has a good price/performance ratio; thermoplastic polyester powder coatings have the advantages of beautiful appearance and high artistry. These properties give thermoplastic powder coatings a large share of the coatings market.
Polyvinyl chloride powder is one of the cheapest polymers to be produced on an industrial scale. It has excellent solvent resistance, good corrosion resistance to water and acid, impact resistance, salt spray resistance, prevents food contamination and has high resistance to electrostatic spraying
Dielectric strength. Mainly used for coating metal mesh panels, steel furniture, chemical equipment, etc.
Polyethylene powder coating has excellent corrosion resistance, chemical resistance and excellent electrical insulation and ultraviolet radiation resistance. The disadvantage is that the mechanical strength is not high and the adhesion to the substrate is poor. It can be used in chemical tanks, impellers, pumps, inner walls of pipes, instrument housings, metal sheets, refrigerator inner mesh panels, auto parts, etc.
Nylon powder coating. Nylon is also known as polyamide. Because the N atom of the chlorine group on the molecular chain and the hydrogen atom on the adjacent segment are easy to form hydrogen bonds, the melting point of polyamide resin is generally higher. Nylon has the advantages of high mechanical strength, impact resistance, hardness, wear resistance, small friction coefficient, and low dust absorption, and can be used for parts with special requirements. Such as pump impellers, textile machinery parts, starting piston parts of diesel engines, sailboat propellers, car wheels, motorcycle brackets, agricultural machinery, construction and sports equipment, etc. In addition, due to nylon's resistance to salt water and inertness to mold and bacteria, it is very suitable for making coatings immersed in seawater or in contact with seawater. At the same time, nylon powder coatings are non-toxic, tasteless, not eroded by mold, and will not promote bacterial growth. Suitable for spraying food industry parts, drinking water pipes and food packaging, etc.
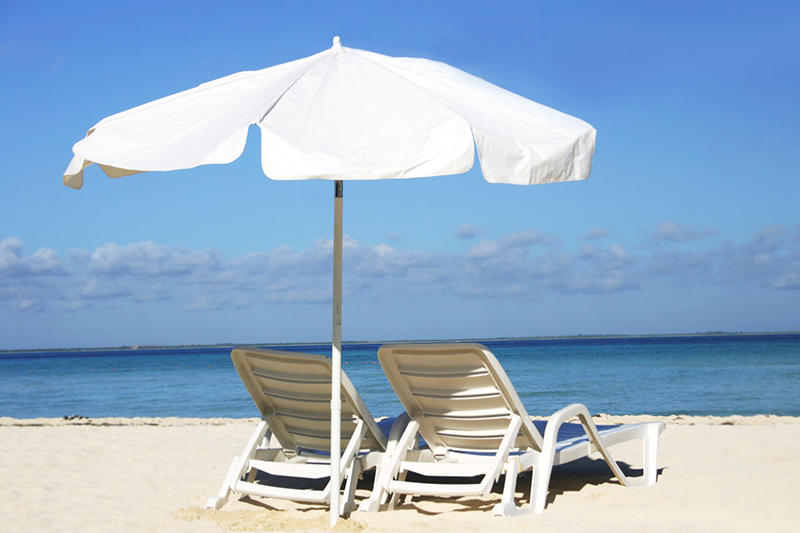
Fluorine resin powder coating. There are many types of fluoropolymers that can be used to prepare powder coatings, such as polytetrafluoroethylene (PTFE), polychlorotrifluoroethylene (PTFCE), polyvinylidene fluoride (PVDF), etc. The melting point of polytetrafluoroethylene is as high as 327 °C, and it can be used for a long time in the range of -250 to 250 °C. In addition, it has excellent corrosion resistance, not even in aqua regia, excellent dielectric properties, extremely low friction coefficient and Self-lubricating, so it is known as the "Plastic King". It is widely used in petroleum and chemical anti-corrosion coatings, seals, bearing lubricating materials, electronic and electrical materials, ship launching rails and non-stick pan coatings. The price of polychlorotrifluoroethylene is cheaper than that of PTFE, the processing temperature can be reduced, the coating can be used for a long time below 130 °C, the corrosion resistance of alkali and hydrogen fluoride is better than that of acid-resistant enamel, and the corrosion resistance of hydrochloric acid, dilute sulfuric acid, hydrogen chloride and chlorine gas. Better than stainless steel equipment. It has been widely used in anti-corrosion equipment in chemical factories, pesticide factories, pharmaceutical factories, detergent factories, etc. The biggest advantage of polyvinylidene fluoride powder coating is that it has excellent weather resistance, high degradation resistance in outdoor exposure, and does not absorb dust, so it is easy to maintain the original gloss. 5 Chlorinated polyether powder coating. Chlorinated polyether has excellent chemical stability. The coating film has good anti-corrosion and anti-dissolution properties to various acids, alkalis and solvents. Its chemical stability is second only to PTFE, and its mechanical and friction properties are also very good. Chlorinated polyether powder coatings are mainly used in chemical equipment, pipeline linings, instrument equipment shells, etc. The disadvantage is poor adhesion to metal. Adhesion to metals can be improved by adding additives.
Latex powder coating
Latex powder is prepared by spray-drying the emulsion, most of which are vinyl acetate copolymers. The paint produced with latex powder is called latex powder coating. It is the most environmentally friendly paint in the current wall paint.